Magnetic Detection of Old Ammunition in the Sea
An estimated 1.6 million tons of ammunition remains from the Second World War are found on the seabed of German waters, which corresponds to around 18.000 wheel loaders. The core components of this ammunition are TNT, white phosphorus, sulfur mustard, tabun, phosgene or arsenic, which, as is well known, are not really health-promoting substances. The longer the ammunition lies on the seabed, the higher the risk of the ammunition casings rusting through and the contents escaping. The consequences of this are devastating and can already be felt today. Entire biotopes are being destroyed and unconscious human contact with the dangerous residues, whether while bathing or working underwater, can lead to serious injuries.
The DAMAS project (DAMAS abbrivates the German project title "Detektion von Altmunition unter Wasser mit magnetoelektrischen Sensorsystemen") was launched to counteract this problem. The task and goal of the project is to develop a prototype for the detection of ammunition on the seabed of the Baltic Sea. The earth's magnetic field is to be used for this purpose. With the help of magnetic sensors, deviations of the local magnetic field from the earth's magnetic field can be measured and evaluated and thus potential ammunition containers can be detected.
Due to the low proportion of women in MINT courses, the CRC 1261 would like to specifically support young women in this area and show them new ways and possibilities of how to tackle exciting research questions in the field of magnetoelectric sensor technology. Therefore, the project is only accessible to female scientists.
We offer you:
- A versatile, challenging project in which you can gain your first practical experience.
- Cross-course contacts with students, but also contact with PhD students, postdocs and professors of the working groups and the CRC.
- An appropriate remuneration for your work.
Requirements:
- You are a matriculated student at the CAU Kiel.
- You are currently enrolled in a STEM program.
- You have about 30 hours a month.
- You enjoy working in a team, are motivated and committed throughout the project.
The studies and the related homework, exams or other time-consuming services are of course still the top priority. If the project and the course overlap, a solution can certainly be found. If we have aroused your interest, please apply to us!
Video
Interview
Team
Currently four students are part of the project. They come from different study programs with different background. A very promising pure female team.
Negar Hosseinimanesh | ||
---|---|---|
![]() |
2020 - today | Materials Science and Engineering (Master), Christian-Albrechts-Universität zu Kiel, Kiel, Germany |
2015 - 2019 | Bachelor of Science – Metallurgy and Material Engineering, University of Tehran, Tehran, Iran | |
"With the background in material science and engineering, I am passionate to participate in interdisciplinary projects that provides me with the opportunity to work beside professional members on a variety of topics. Working as a member of “Damas” project serves me an exposure to an understanding certain principle and an overview of subjects in broader scope of material science field, with the great mission of protecting environment." |
Marlene Markus | ||
---|---|---|
![]() |
2022 - today | Materials Science and Business Administration (Master), Christian-Albrechts-Universität zu Kiel, Kiel, Germany |
2018 - 2022 | Wirtschaftsingenieurwesen Materialwissenschaft (Bachelor), Christian-Albrechts-Universität zu Kiel, Kiel, Germany | |
2009 - 2018 | Allgemeine Hochschulreife, Gymnasium Allee, Hamburg, Germany | |
"I'm motivated by working and developing solutions in a team. With this project I´m especially looking forward to network with other women from different fields of expertise, learn from each other and challenge each other. The combination of environmental and technical research makes the project inevitable and very relevant to the future." |
Katsiaryna Tsishchankava | ||
---|---|---|
![]() |
2022 - today | M.Sc. in physics at the Christian-Albrechts-Universität zu Kiel, Kiel, Germany |
2014 - 2019 | Diploma in physics, Belarusian State University, Faculty of Physics, Minsk, Belarus | |
2007 - 2014 | Gymnasium No. 1, Novogrudok, Belarus | |
"I see the project DAMAS as a good opportunity to contribute to a safer and cleaner environment, while at the same time improving my skills as a researcher." |
Martyna Wrobel | ||
---|---|---|
![]() |
2021 - today | B.Sc. in Electrical Engineering at the Christian-Albrechts-Universität zu Kiel, Kiel, Germany |
2020 | Abitur, Pestalozzi-Gymnasium, Guben, Germany | |
"Working in a team is a very important skill that every electroingenieur needs. The DAMAS Project is a great opportunity, to work on environmentally important topic, with a various group of people and get a better understanding of what the future holds for me." |
Former Members
Two students have already left the project. Karoline Gussow has found a PhD position in department of electrical engineering in Kiel. She continues her research on underwater signal processing, but now with acoustic sensors. Nadja Dreier is focussing now on finishing her bachelor degree.
Nadja Dreier | ||
---|---|---|
![]() |
2018 - 2023 | Wirtschaftsingenieurwesen Elektro- und Informationstechnik (Bachelor), Christian-Albrechts-Universität zu Kiel, Kiel, Germany |
2009 - 2017 | Abitur, Friedrich-Schiller- Gymnasium, Preetz, Germany | |
"Even though my studies in economical engineering are coming to a close within the next few semesters, practical application has only been a minor topic so far. When I recieved the e-mail inviting me to the program I felt like it would present that opportunity to me - Gain further knowledge, experience and a way to use the so far only theoretical skills." |
Karoline Gussow | ||
---|---|---|
![]() |
2021 - 2022 | Master program in Electrical Engineering and Business Administration at the Christian-Albrechts-Universität zu Kiel, Kiel, Germany |
2017 - 2021 | B.Sc. in Electrical Engineering and Business Administration at the Christian-Albrechts-Universität zu Kiel, Kiel, Germany | |
2014 - 2017 | Apprenticeship as industrial management assistant at Stadtwerke Kiel AG, Kiel, Germany | |
"I am participating in the DAMAS project because I was convinced by the environmental and health aspects behind this project. In addition, I am very interested in underwater signal processing and have therefore already dealt with it at the end of my bachelor's degree and during my master's degree. The project offers me a further deepening in this direction and I can contribute to the Baltic Sea being less polluted by old ammunition." |
Project Progress
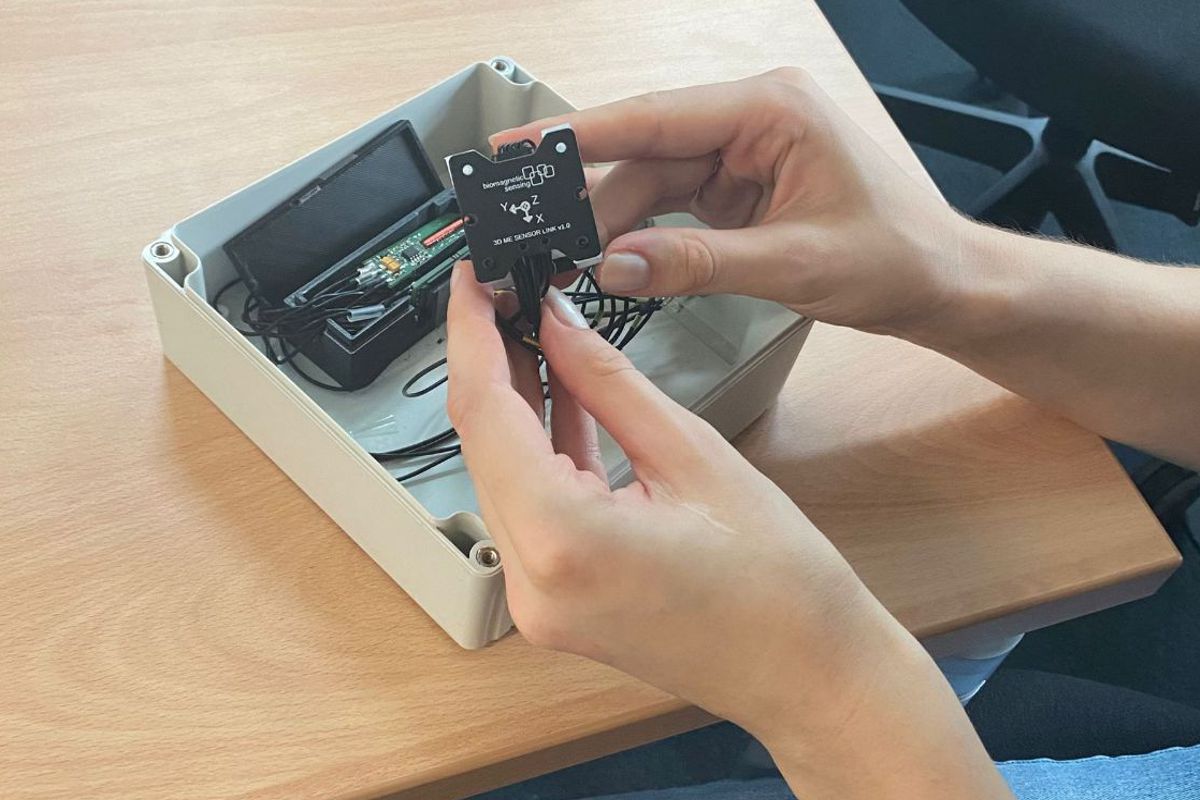
The PC-based group has finished soldering all the connecting cables, polished the boxes for ME sensors and circuit boards and connected them with each other. All connection points were tested to prevent short circuit. That means, that both fluxgate and ME sensors are ready to be tested together. The first step in this direction will be to test them on the surface and if this test is successful, the prototype can be put underwater to prove its performance there.e of these errors was identified to be functionality issues with the wires.
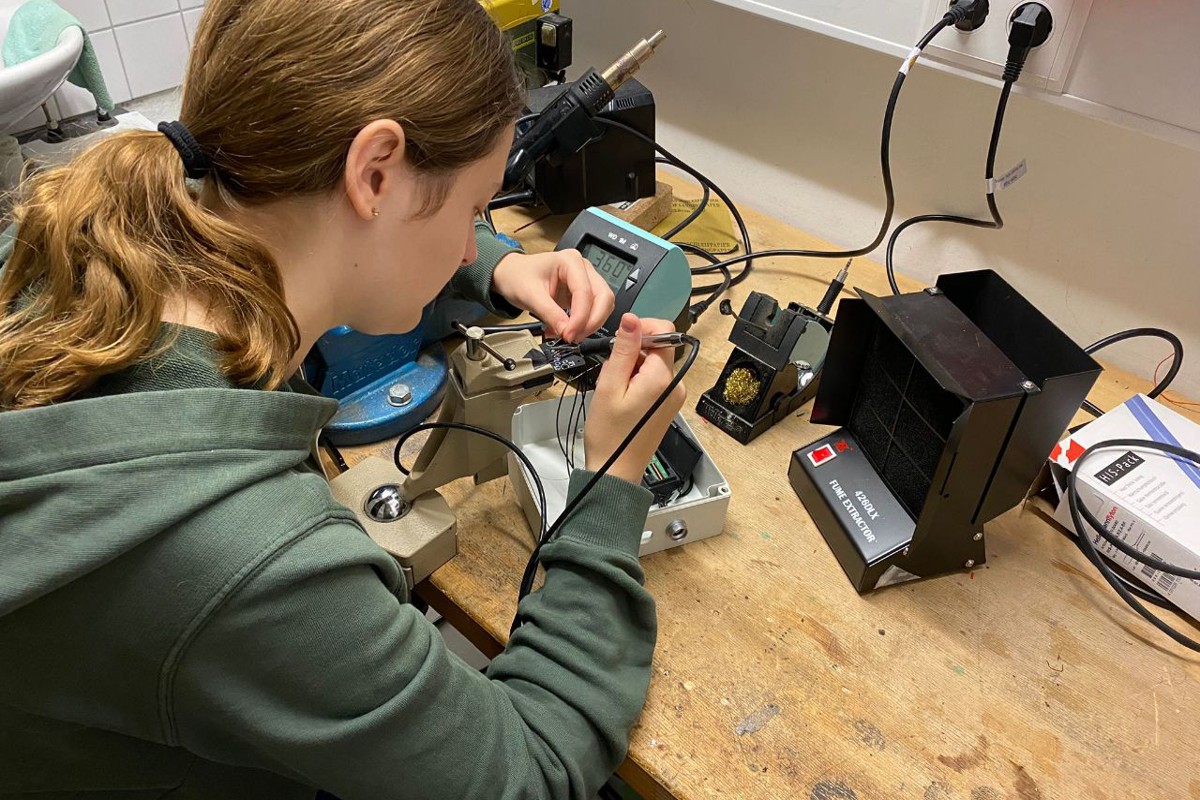
The PC-based group received the circuit boards for the ME sensors and was able to proceed with the subsequent implementation steps. The team's objective was to solder these circuit boards, rendering all used cables compatible with both sensor types: ME and fluxgate. To achieve this, the cable pins needed to be soldered to the appropriate sensor connectors, thus preventing any inadvertent signal to the X, Y, or Z channels.
Due to the distinct output and input signal requirements of these sensors, the team prepared two distinct cables for each ME sensor, designed to connect them to the PC: one for 12 V and another for -12 V. The next steps entail the preparation of three additional connecting cables, connecting the ME sensors with the circuit boards and conducting tests to determine the accuracy of the output signals.
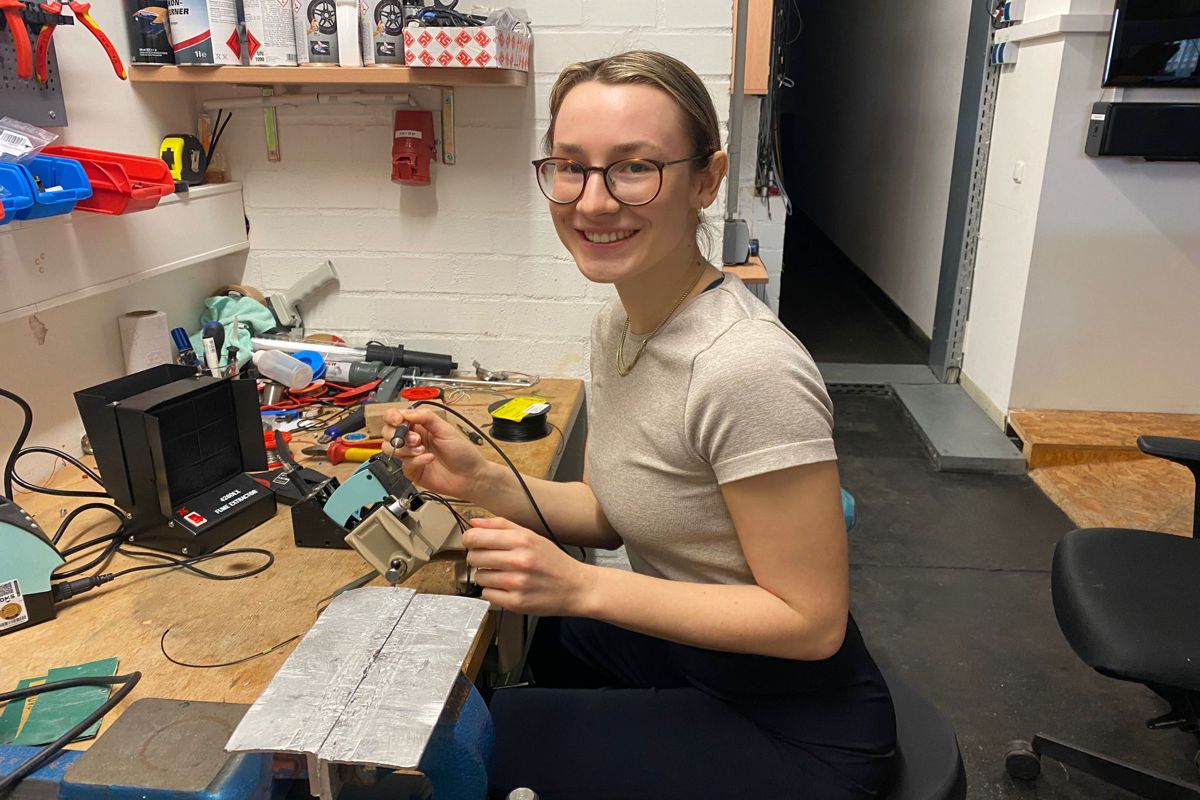
With the new Curiosity LPC board in place, seamless communication between the microcontroller, amplifier, and SD-card board was achieved. Rigorous testing and debugging were carried out, resulting in a fully functional system without any errors in the program part.
In the subsequent phase, the team undertook the critical task of verifying if the SD card effectively stored the received signals. To accomplish this, an analog signal was produced using an oscilloscope. The ADC part of the microcontroller performed impeccably, converting the analog signal into digital format. These digital signals were then successfully stored in the SD card and confirmed to be readable.
In the previous week the PC-based group took care of the hardware once again. Some preparations still needed to be made so that the ME sensors could be placed inside the box.The first step that the group took was drilling another hole in the outer boxes, so that there is one pin connector for the fluxgate sensors and two pin connectors for the ME sensors. Following that, cables were soldered to the designated pins for the ME sensors. The final step involved examining the circuit boards and discussing and finalizing the pin assignment. Once the ME sensors are ready for operation, the group will solder them to the prepared cables.

During the last month, significant efforts were directed towards coding the microcontroller. Unfortunately, several obstacles were encountered due to poor connections between the microcontroller, SD-card chip, and Pickit (the programmers for PIC microcontrollers). The root cause of these errors was identified to be functionality issues with the wires.
To address the challenges posed by the previous board, the decision was made to procure a Curiosity LPC board from Microchip Technology Inc. The Curiosity LPC board supports 20-pin 8-bit PIC® Microcontrollers with low voltage programming capability. This transition eliminated the need for an extra PicKit, which had been a major source of trouble in the previous setup.
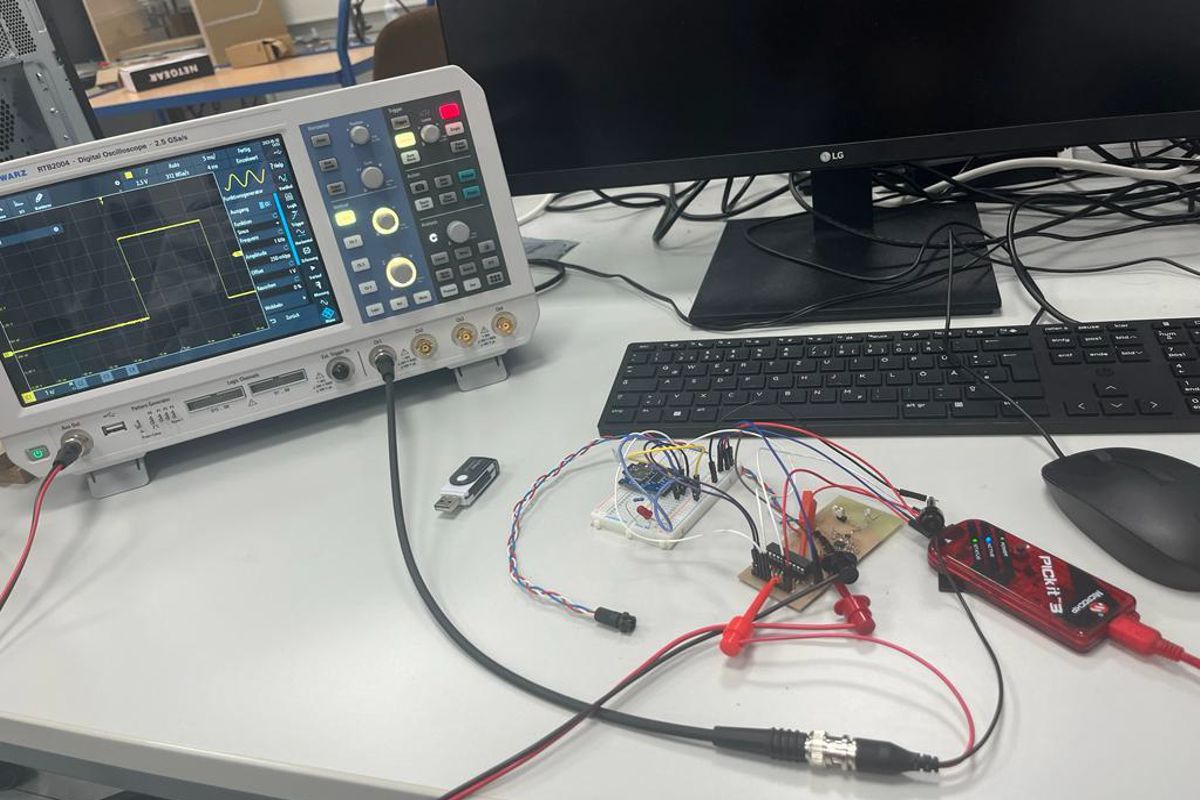
The main focus of the "embedde group" has been on integrating the microchip memory with the microcontroller board and coding the memory card to store the microcontroller data. They started by carefully selecting the appropriate microSD cardboard that could efficiently handle the data storage requirements of the microcontroller. Once they had identified the right memory chip, they proceeded to integrate it with the microcontroller board. Next, they began coding the memory card to ensure it could store all the data generated by the microcontroller. This involved working with a c programming language and MPlab tool to develop a customized solution that was tailored to the specific needs of our project. They have made significant progress in both areas, and the memory card is now fully operational, successfully storing all the data generated by the microcontroller. Moving forward, they plan to test the memory card extensively to ensure it is stable and reliable and refine our coding and testing processes to optimize the performance of the Memory card.
The "PC-based group" coducted measurement using a fake bomb with distances of approximately 10, 20, and 40 cm from our sensor box. The measurements revealed that a distance of 40 cm for the fake bomb was too far, as no signals could be detected anymore. Additionally, the ME sensors were calibrated, and preparations were made for the cube circuit board to which the ME sensors will be attached.
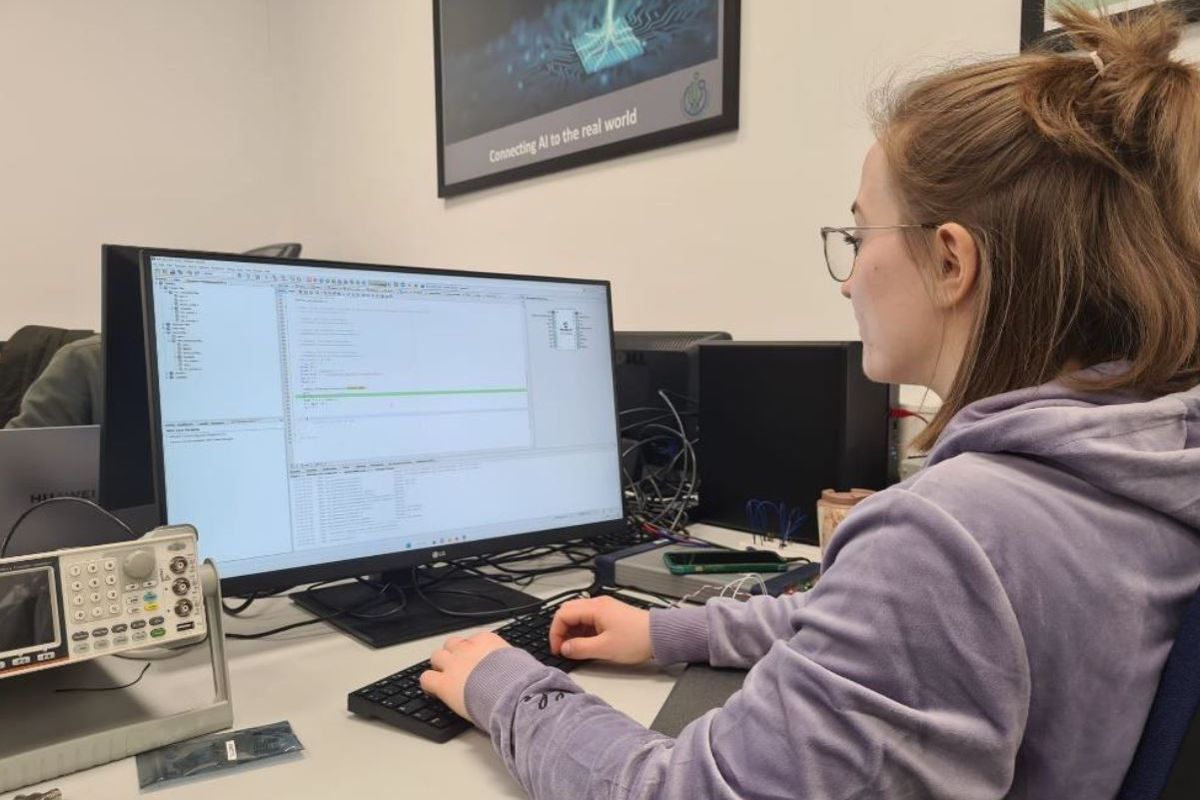
After completing and improving the hardware for the fluxgate sensors, the ("PC-based") group was planning the next steps, which include working not only with fluxgate sensors but also with ME sensors. The imitation of a bomb was prepared to simulate the change in the magnetic field of the Earth. Some tests were done to understand, how the signals from fluxgate sensors would look like. Two boxes with fluxgate sensors in them were placed at a fixed distance from each other and the "bomb" was driven over it. The changes in signals could be seen, when the sensors were very close to the "bomb". Next, the group will look at the possibilities of the software (KiRAT), to see how these signals can be processed.
The "embedded group" are pleased to report that significant progress has been made in programming the microcontroller since our last update. Our team has been dedicated to coding and debugging the analog-to-digital conversion aspect of the microcontroller. In order to ensure proper functionality of the signal conversion, a reverse code was utilized to convert digital signals to analog signals, which were then analyzed using an oscilloscope. Through these efforts, we have successfully confirmed the proper functioning of the ADC and DAC components of the microcontroller.
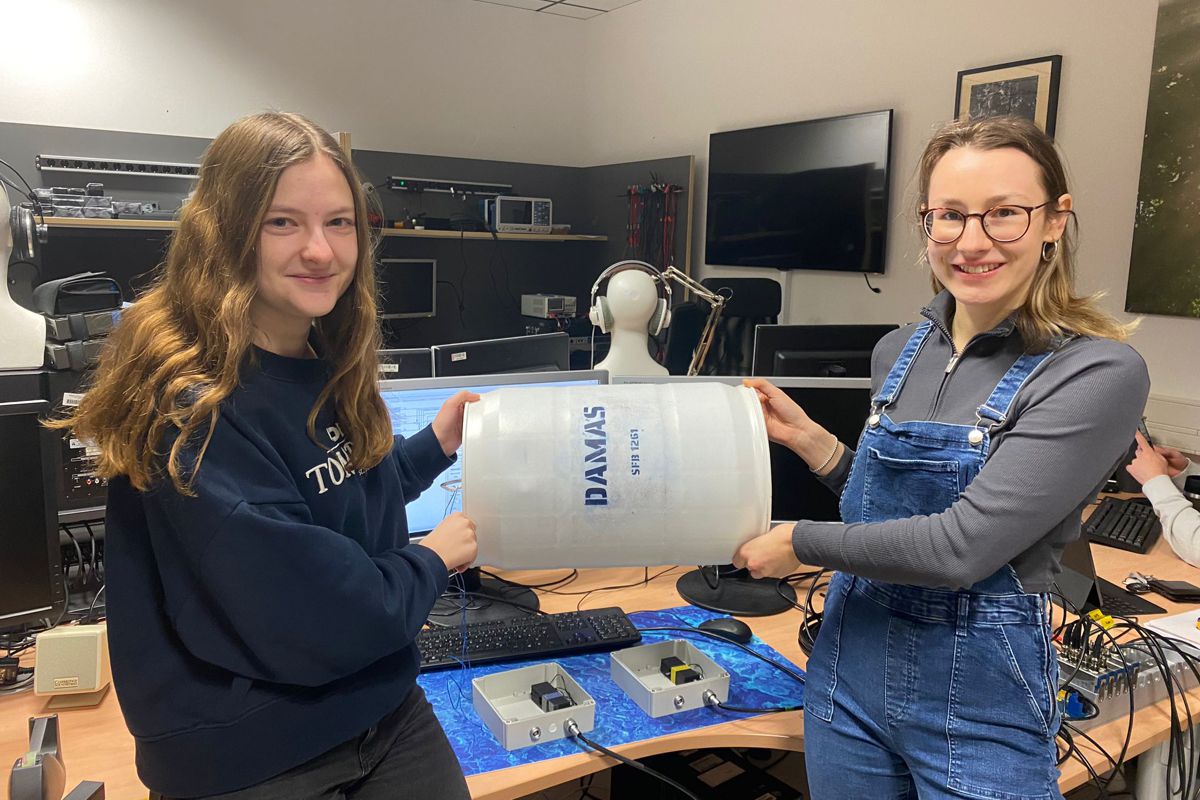
After completing and improving the hardware for the fluxgate sensors, the group was planning the next steps, which include working not only with fluxgate sensors but also with ME-sensors. The imitation of a bomb was prepared to simulate the change in the magnetic field of the Earth. Some tests were done to understand, how the signals from fluxgate sensors would look like. Two boxes with fluxgate sensors in them were placed at a fixed distance from each other and the "bomb" was driven over it. The changes in signals could be seen, when the sensors were very close to the "bomb". Next, the group will look at the possibilities of the software (KiRAT), to see how these signals can be processed.
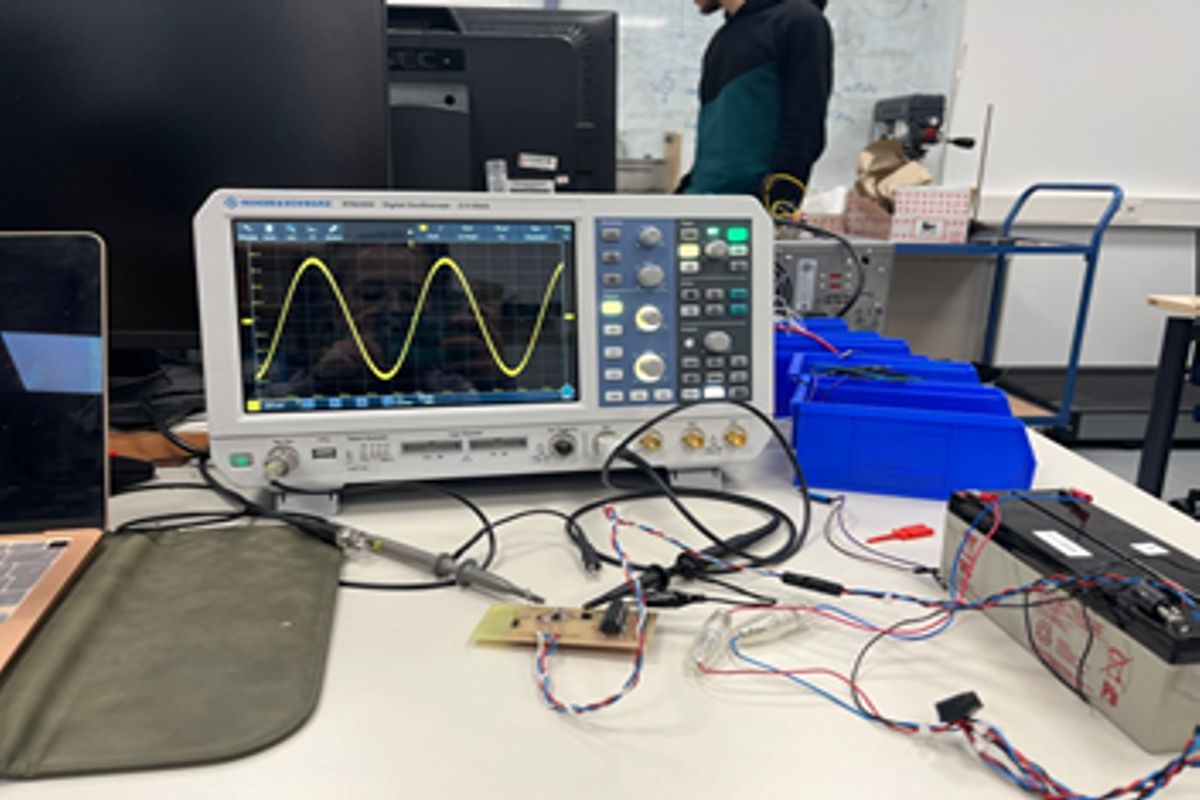
In the last weeks focus of the work of "the embedded group" was debugging the PCB. The next step after preparing PCB was testing functionality of the different parts. In this stage some problems have been found by amplifier, so we spent couple of days looking from different perspectives to find out the problems. In this regard, we found one ground connection which was not properly soldered which caused problems. Now by solving this problem we could start with programing of the microcontroller.
On the meeting with Professor Rieger we discussed operation of the microcontroller. We have planned to connect sensor and micro SD-card reader to examine the whole process with sensors. Also we came to the point of adding two resistors. We need the resistors to shift average value of the output amplified signal due to the limited range of microcontroller power (0V-5V). We wish to have a ready prototype which we could connect with the project of the other group at the end of this month.
In recent weeks, the "PC-based" group has been working on improving the performance of their sensor system through a series of controlled experiments. To establish a reliable baseline, they conducted magnetic field measurements in dry conditions, which allowed them to analyze the system's performance without interference of external factors. After evaluating various options, they selected an epoxy lining for the larger box, which provides a protective barrier against water intrusion. In addition to ...
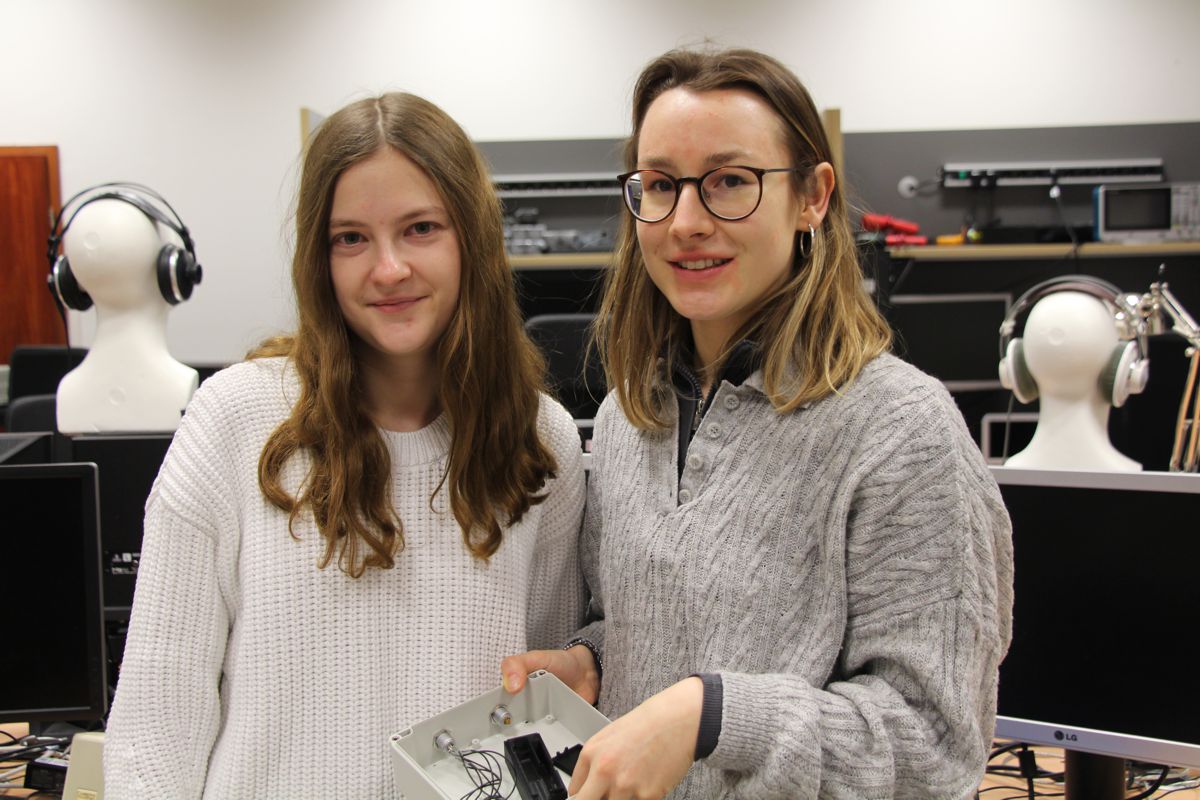
The PC-based group has been working to address technical issues with the hardware. Through a series of iterative improvements and thorough testing, the team was able to identify and successfully rectify the core problem, which was caused by incorrect connections between two output channels. As a result, it is now possible to make measurements using two boxes. The initial tests were performed using the program KiRAT, but these were only conducted on the surface and not underwater. However, further tests are planned, including those to be made under water, to ensure the reliability of the measurements. Additionally, to guarantee optimal performance, some hardware components such as cables were also renewed and soldered. The team also evaluated the current functionality of KiRAT and is taking steps to enhance it for the purpose of detecting weak signals during underwater measurements.
Embedded group: in the last weeks were basically the winter holidays and in the beginning of 2023 the project get a new member. So we meet together an tell her about our workflow in the last months and what we want to do in the future. The next steps will be to build up a water resistant box and program the micro controller on our PCB, so that the bomb searching is possible.
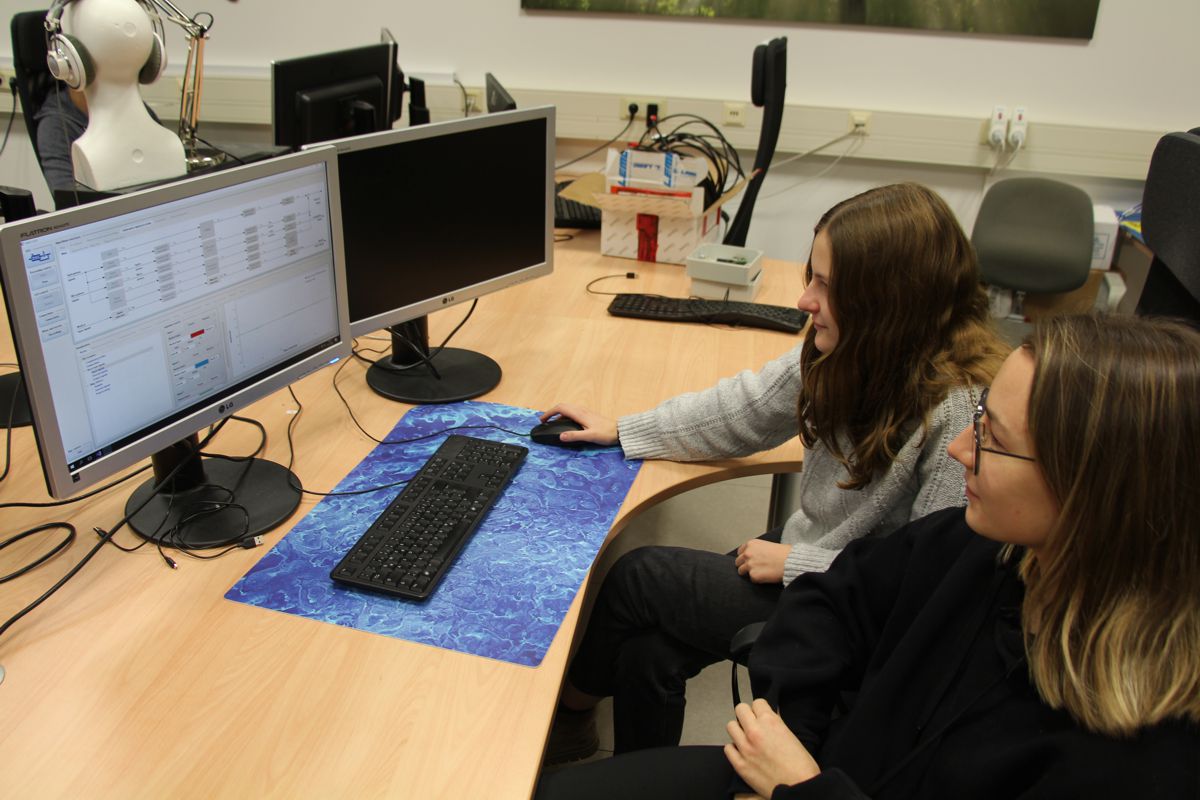
In this month the PC-based group was dealing with issues regarding the connectivity between the fluxgate sensors and the PC. In a series of iterative improvements and performed tests the core problem was identified, which was caused by mixed up connections between two output channels. Another performance test was planned.
Additionally, the existing functionality of KiRAT was assessed and thoughts were put into further improvement of the software for the specific task of detecting weak signals during the underwater measurements.